Blog Title: Technical Requirements for Adhesive Label Processing: Common Labeling Issues and Solutions
Adhesive labels, though often overlooked, are an integral part of packaging across industries. Whether it’s a bottle of wine, a cosmetic container, or a pharmaceutical product, the label serves not only as an information carrier but also as a branding tool that can influence consumer decisions. In this blog post, we'll delve into the complexities of adhesive labels and the techniques that ensure they adhere flawlessly to their intended surfaces.
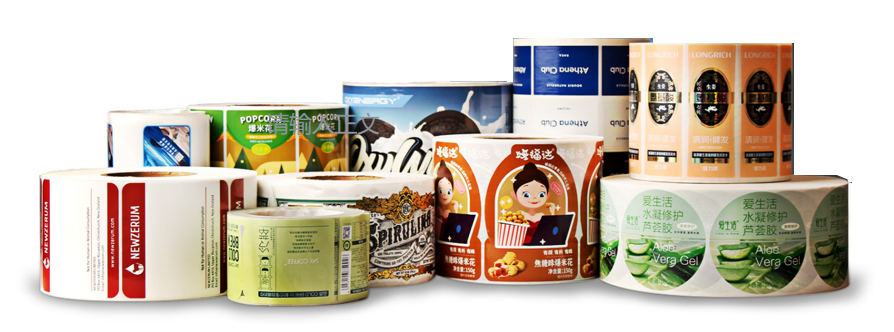
Why Customers Have Label Processing Requirements?
When customers request adhesive labels, they often have specific requirements tailored to their products and the machinery used in their production lines.These requirements can include the diameter of the finished label roll, the direction in which the labels are dispensed, and even the spacing between labels. Meeting these requirements is crucial to ensure that the labeling process is efficient and error-free.
Roll Diameter:
The diameter of the label roll is influenced by the storage capacity of the labeling machine. Standard diameters on the market typically range between 250mm, 320mm, and 420mm. The larger the roll, the more labels it contains, reducing the need for frequent roll changes and increasing production efficiency.
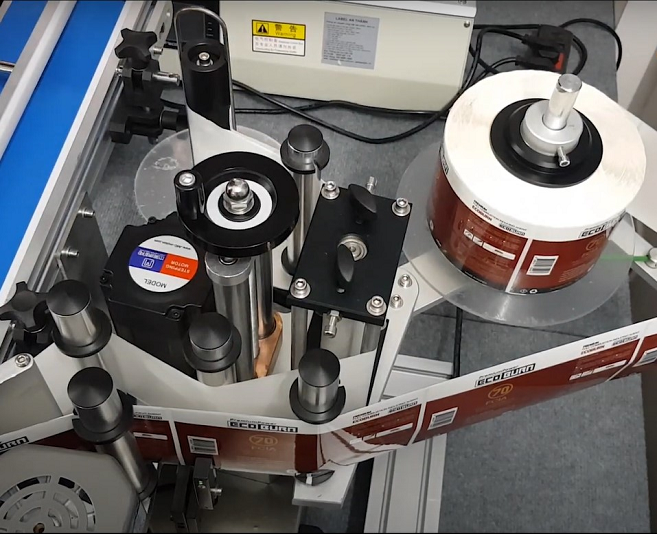
Label Dispensing Direction:
Labeling machines have fixed components, and if the label’s dispensing direction does not align with the machine’s specifications, the labels cannot be applied correctly.
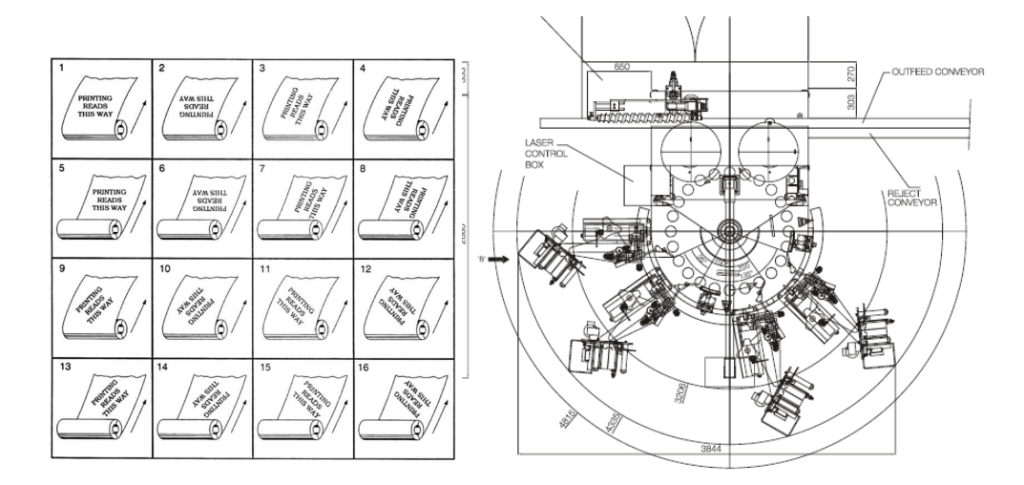
Label Spacing: Optimal label spacing is about 3mm, with the minimum spacing not less than 2.5mm. Incorrect spacing can lead to misalignment and even missing labels during the application process.
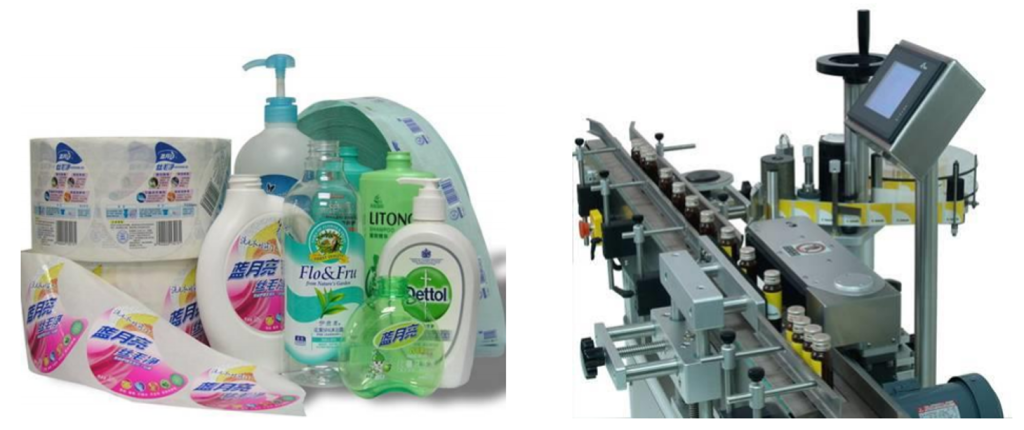
Key Factors for Labeling Different Bottles
The shape of the bottle plays a significant role in determining how a label should be applied. Each bottle shape presents unique challenges:
Flat Bottles: Common in the personal care industry, these bottles often use HDPE or PET materials. HDPE bottles can be difficult to label due to their curvature, which may lead to deformation during labeling. PET bottles, particularly when using transparent labels, require a flawless application to avoid visible air bubbles and other imperfections.
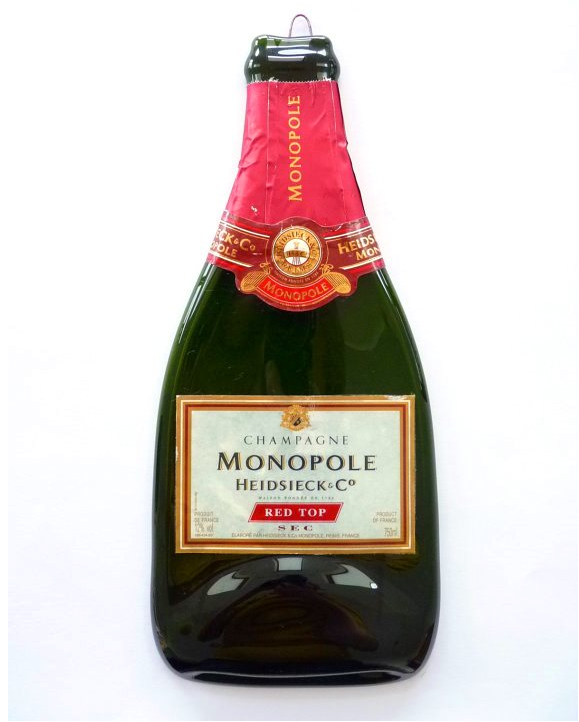
Round Bottles: Labeling round bottles, especially large ones, requires precision to ensure that the label wraps smoothly around the entire circumference without misalignment. Techniques like using a rotating platform or adjusting the label design to include rounded corners can help reduce visual errors.
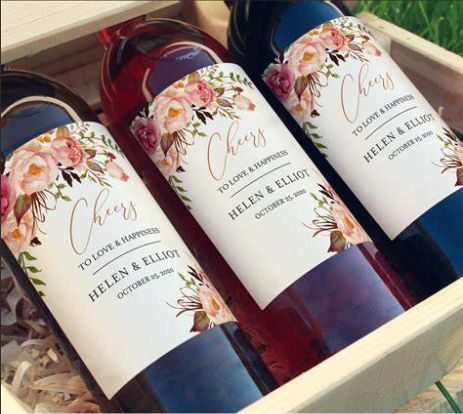
Square Bottles: Square bottles present the challenge of applying labels on three or four sides without the ability to rotate the bottle. This requires pre-peeling all labels and ensuring that the corners are rounded to minimize visual discrepancies.
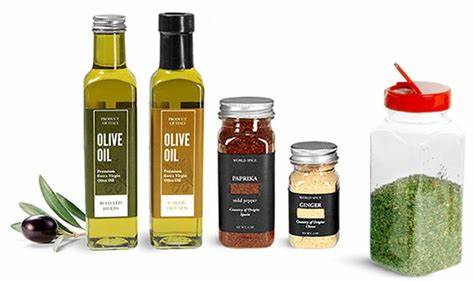
Cone-Shaped Bottles: Labeling cone-shaped bottles is tricky due to the tapering sides. Labels must be designed with a fan shape, and the starting point of the label should align with the generatrix of the bottle.
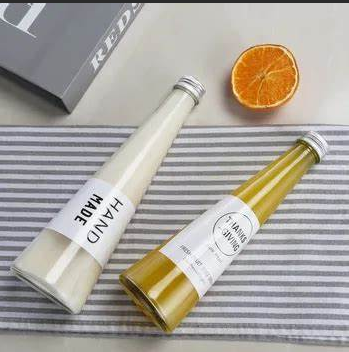
Soft Tubes: Tubes, often used for creams and gels, pose challenges such as edge lifting due to the curvature at the sealed end. A solution is to design the label with a curved edge that stays away from the tube’s seal.
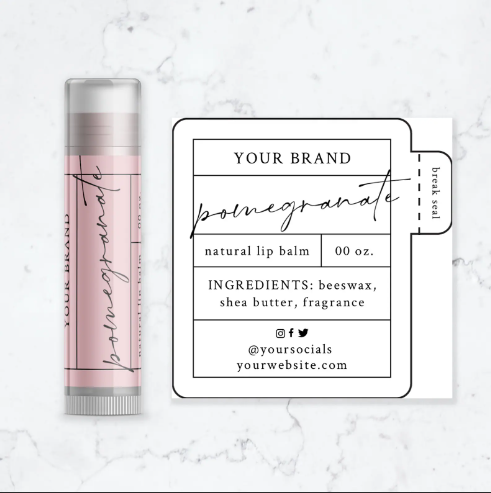
Common Labeling Issues Explained
Despite best efforts, anomalies can occur during the labeling process, often resulting from factors related to the bottle, label material, adhesive properties, or the environment. Common issues include:

Label Lifting: This can result from inadequate stiffness of the label material, poor adhesion of the glue, or an uneven surface on the bottle. Adjusting the pressure applied during labeling or selecting a more suitable adhesive can mitigate this issue.
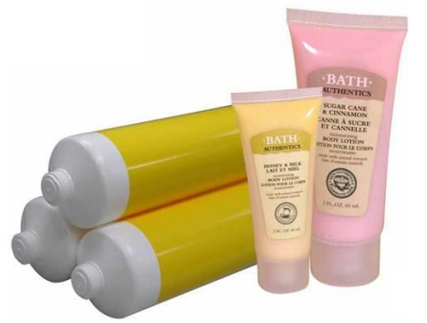
Label Wrinkling: Wrinkling is often due to mismatched speeds between the label dispensing and the bottle's movement, or the use of unsuitable bottle shapes. Ensuring that the labeling machine is properly calibrated can prevent wrinkles.
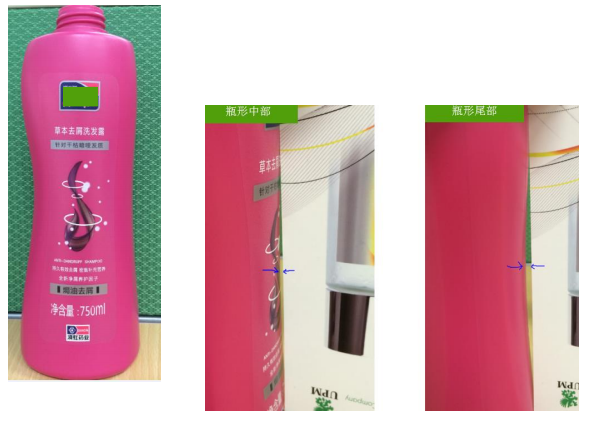
Air Bubbles: Air bubbles under labels can be caused by the bottle's surface being too rough or the label material being too stiff. Using a scraper to apply consistent pressure can help eliminate bubbles.
Label Breakage: Label breakage is typically due to inadequate strength of the backing paper or excessive tension during application. High-speed machines are particularly prone to this issue, requiring careful selection of materials and machine settings.
Advanced Solutions for Labeling Challenges
Modern labeling technologies and materials offer solutions to many of the common challenges in the industry. For instance, high-speed labeling machines now use PET backing paper that is more durable and compatible with various label materials. Additionally, temperature-controlled storage and advanced adhesive formulations ensure that labels adhere securely, even under extreme conditions.
In conclusion, the science of adhesive labeling is intricate and multifaceted. From understanding customer requirements to tackling the challenges posed by different bottle shapes and addressing common anomalies, every aspect requires careful consideration and precise execution. As the packaging industry continues to evolve, so too will the technologies and techniques that ensure labels are applied perfectly every time.
